Smart Envelope Systems With Integrated Smart Envelope Materials and Facilities to Achieve Zero-Energy Buildings
Smart Envelope Systems With Integrated Smart Envelope Materials and Facilities to Achieve Zero-Energy Buildings
▲ Postdoctoral Researcher Lee Hyun-hwa, Department of Building Energy Research, KITC
Prologue
Following the 2019 UN Climate Action Summit, the policy agenda of achieving carbon neutrality by 2050 began to gain prominence. Europe and the United States have set carbon neutrality targets, while China has declared its commitment to achieving carbon neutrality by 2060. In Korea, the government's 2050 Carbon Neutrality Promotion Strategy includes a roadmap for carbon neutrality in the building sector. In 2023, zero-energy building requirements have been expanded to include public buildings larger than 500 m² and public housing projects with more than 30 units. There also is a growing movement to transform aged buildings, which constitute 74% of the total building stock, into zero-energy buildings through initiatives like Green Remodeling. The gradual enforcement of zero-energy building requirements is underway.
This movement is a global trend, and the IEA FTS (International Energy Agency's Faster Transition Scenario) predicts a 75% reduction in greenhouse gas emissions through investments in energy-efficient measures in the building sector. This is expected to create a domestic market worth approximately KRW 80 trillion for new construction and remodeling, while the global market for zero-energy buildings is projected to reach approximately USD 1.3 trillion by 2035.
The transition of current architectural technologies toward future technologies is hindered by certain limitations. In particular, there are limitations to the extent to which both passive and active single-element technologies can be advanced, and there has been a decline in construction quality due to joint defects caused by sequential on-site construction. Additionally, existing control systems are inadequate when it comes to responding quickly to environmental changes.
As a result, there is a growing need for smart envelope systems that can overcome these limitations by incorporating smart envelope materials and facilities. These systems should address issues such as energy efficiency, comfort, and design, while considering energy, safety, and business feasibility through prefabrication and modular construction methods. This article aims to introduce the current status of technological development for smart envelope systems integrating smart envelope materials and facilities, both at home and abroad.
Current Status of Technological Development for IUES of Envelope Materials and Facilities in Other Countries
One example is the MVHR-μHP testbed case, which was part of the iNSPiRe project conducted in 2015. The project verified the performance of the building envelope, small-scale heat pumps, and ventilation systems. Ultimately, its advantage lies in its minimization of the space utilization of the machine equipment installation location on the interior side by using an assembled prefabricated envelope and installing it as an integral wall, thereby reducing the air path.
The MORE-CONNECT project is a test bed and demonstration project that applies a developed converged envelope in several European countries, including Denmark and Estonia. It is a project in which remodeling was performed linking renewable energy on the wall and roof surface corresponding to the envelope. In the Danish demonstration case, the PV (Photovoltaics) panel and the roof-integrated module is utilized in the remodeling demonstration. As a result, it can be confirmed that the renewable energy and the electrical system are organically connected to the outer wall. The Estonian demonstration is a case study in which a prefabricated factory-manufactured wood frame module system, combined with an envelope material that incorporates various facility technologies and a renewable energy system, was used to remodel an apartment housing complex with a concrete structure. During the remodeling process, changes were made to the high-performance insulation envelope, balcony reconstruction, heating system, and ventilation system. In addition, solar power and solar thermal renewable energy sources were utilized. This is an example of continuous monitoring being conducted through the building's monitoring system.
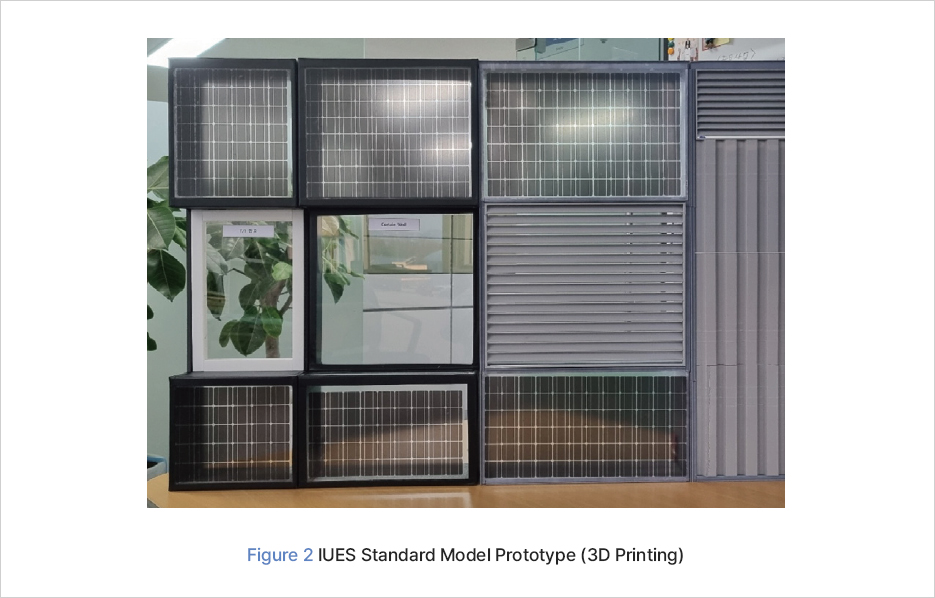
Current Status of Technological Development for IUES of Envelope Materials and Facilities in Korea
The Korea Institute of Civil Engineering and Building Technology (KICT) has conducted a research project entitled "Empirical Study on the Development of Smart Cladding and Facility Convergence Technology for Achieving Zero-Energy Buildings and Establishment of a Performance Evaluation System," which was supported by the Korea Institute of Energy Technology Evaluation and Planning (KETEP). In this research, the Incremental Unitary Envelope System (IUES), an exterior material and facility convergence module system, was developed. Its performance was validated through testing in a testbed, and it is now being prepared for implementation in a real-world demonstration site. The IUES, while combining the cooling and heating system with the interior materials of the building, aims to maximize energy efficiency by utilizing various energy sources, such as renewable energy, and implementing AI-based integrated control.
The KICT has selectively integrated five core technologies and 26 detailed technologies, including exterior material technology, facility technology, optimal operation technology, integrated quality certification system establishment, and life cycle management system development to make up units. After combining these units into a unified exterior module, it successfully completed the design, prototype, and testbed application of the standard model for the Smart Cladding and Facility Convergence Module System.
The Smart Cladding and Facility Convergence Module System offers a number of advantages that include improved on-site safety through mitigating the risks associated with factory production, transportation, and easy installation. It ensures construction quality through prefabrication, and enables cost-effectiveness by shortening the construction period.