Development of Nondestructive Evaluation Technology for PSC Structures (PSC Stethoscope)
Development of Nondestructive Evaluation Technology for PSC Structures (PSC Stethoscope)
▲ Senior Researcher Park Kwang-yeun, KICT Department of Structural Engineering Research
The Aging of PSC Structures and Need for External PS Tendon Nondestructive Testing
Whether at home or abroad, in countries where civilization has progressed rapidly, a number of bridges containing the essence of civil engineering technology have been built, allowing logistics and passengers to quickly cross rivers and valleys. In South Korea as well, befitting a civilized country, many bridges have been built and are playing numerous roles. These bridges enable convenient crossing of the Han River to bind the Gangbuk and Gangnam areas into a single city, overcome mountain valleys to greatly increase accessibility to mountainous regions, and connect islands to the mainland. It is found that 38% of these bridges were built using pre-stressed concrete (PSC) structures. Given the fact that a large number of bridges have been built since the 1980s and 1990s when Korea's economy grew rapidly, it can be assumed that the development of safety diagnosis technology for PSC structures older than 30 years is urgent. As the name suggests, the pre-stressed tendon (PS tendon) plays the most critical role in the PSC structure. PS tendons can be broadly classified into external PS tendons and internal PS tendons. For example, regarding external PS tendons, there was a case of enormous economic and social loss in 2016 due to corrosion of external PS tendons on Jeongneungcheon Viaduct, the inner ring road in Seoul, raising public awareness of the need for safety diagnosis (Figure 1).
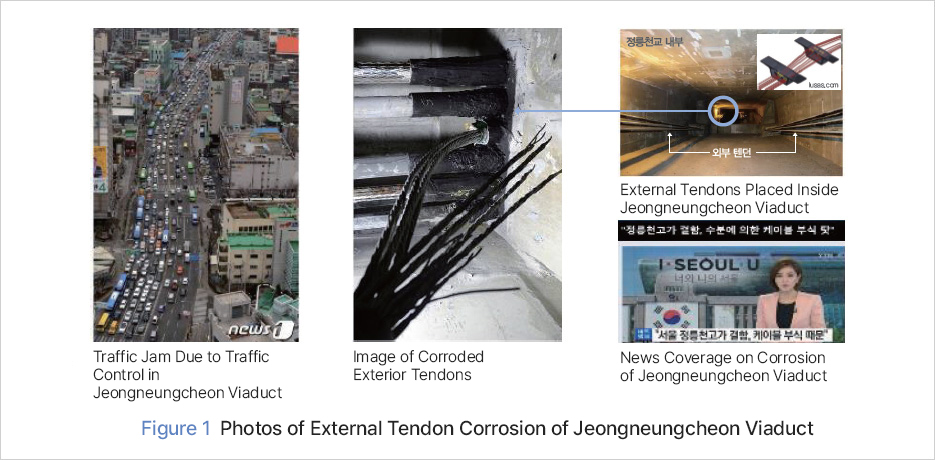
State of External PS Tendon Nondestructive Testing Technology
Taking the Jeongneungcheon Viaduct case as an opportunity, the Korea Institute of Civil Engineering and Building Technology (KICT) conducted the KICT Blind Test (2016), targeting domestic and foreign nondestructive testing technologies to investigate the technology that can assess the integrity of external PS tendons. The integrity of the external PS tendon can be checked using three indicators: sectional damage, stress, and voids. However, for stress, no organization possessed the related technology, regardless of location at home or abroad, and for voids, only one French company (Advitam) applied for and demonstrated a detection rate of about 73%. Among the three indicators, cross-sectional damage is the most important and direct indicator. Of the ten local and foreign companies that applied for related nondestructive technology, only two companies, Tokyo-Rope of Japan and Instron of Russia, showed valid results, and none of the Korean companies demonstrated valid results. As for the technology of the two companies, which showed valid results, we came to the conclusion that it would be difficult to apply it in the field unless the cost, usability, size, and weight of equipment were improved.
Development of Nondestructive Evaluation Technology for PSC Structures (PSC Stethoscope)
For this reason, the KICT initiated a study to develop a proprietary technology that can inspect cross-section damage, stress state, and voids by conducting nondestructive testing of external PS tendons. The cross-sectional damage and stress use the magnetic properties of the external PS tendon made of metal, and the presence or absence of voids is inspected by applying radar technology. In this article, I would like to briefly introduce a technology for nondestructive testing of sectional damage, which is the most important indicator to assess the integrity of PS tendons.
Underlying Concept of Nondestructive Testing Sensor
Figure 2 shows the conceptual diagram of the developed electromagnetic sensor installed on the external PS tendon. Although the external PS tendon (the red-brown part in Figure 2) is actually paved with ducts and grouts, the magnetic properties of the duct and grout are almost the same as that of air (or vacuum). Therefore, it can be assumed that there is no magnetic property. The electromagnetic sensor is largely made up of three parts: the primary coil (yellow part in Figure 2), the secondary coil (orange part in Figure 2), and the fixing frame (purple part in Figure 2). The fixing frame is made of plastic that does not respond to magnetic fields. The primary coil is a kind of electromagnet that generates a magnetic field inside the sensor by flowing electricity, and the magnitude of the generated magnetic field is a function of the cross-sectional area of the external PS tendon, a metal component that penetrates the inside of the sensor. The secondary coil is wound to wrap the external PS tendon several times, and if the magnetic field inside the sensor is changed by varying the current applied to the primary coil, an induced current proportional to the magnetic field change is generated in the secondary coil. Using this principle, when AC electricity having a sine wave shape of constant amplitude is passed through the primary coil, AC electricity having an amplitude positively correlated with the cross-sectional area of the external PS tendon is induced in the secondary coil. Therefore, the cross-sectional area of the external PS tendon can be estimated by analyzing the amplitude of the induced AC electricity. The cross-sectional area of the metal component decreases when the external PS tendon is broken or rusted (iron oxide does not respond to a magnetic field). So, it is possible to estimate corrosion and break from the reduction in the cross-section.
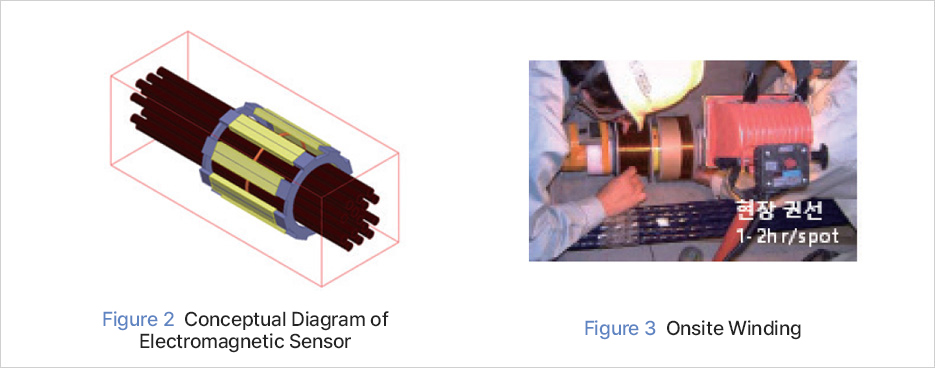
Development of Sensors Optimized for Field Work
As can be seen from Figure 2, the sensor using this principle should have a closed circuit that wraps the external PS tendon. Tokyo-Rope of Japan and Instron of Russia, who were introduced earlier, also share the concepts and basic ideas mentioned above (of course, if you look at the details, they are quite different). However, Japanese and Russian technologies require winding work or equivalent work at the site, as shown in Figure 3, to make a closed circuit wrapping the external PS tendon, which takes a considerable amount of time. Consequently, workability is poor. In addition, since the sensor condition changes every time it is installed, the reliability of the sensor is lowered, and it is disadvantageous to work in the narrow passageway inside the bridge because all the sensor parts must be carried separately to be moved. On the other hand, the electromagnetic sensor developed by the KICT is divided into two, as shown in Figure 4, so with a little mastery, it can be installed within one to two minutes. Furthermore, it was ensured that the reliability of the sensor does not decrease, no matter how many times it is repeatedly installed, by composing the main junction with a highly reliable ready-made connector. The total weight is 5 kg and each side weighs about 2.5 kg, so it is not too heavy for a person to carry. If this sensor is installed as shown in Figure 5 and scanned at an appropriate speed along the external PS tendon, the change in the cross-sectional area can be inspected by performing a nondestructive test for the concerned section.
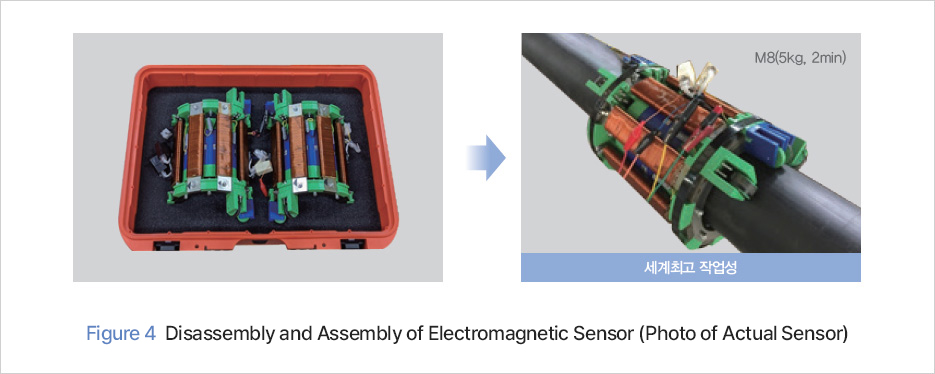
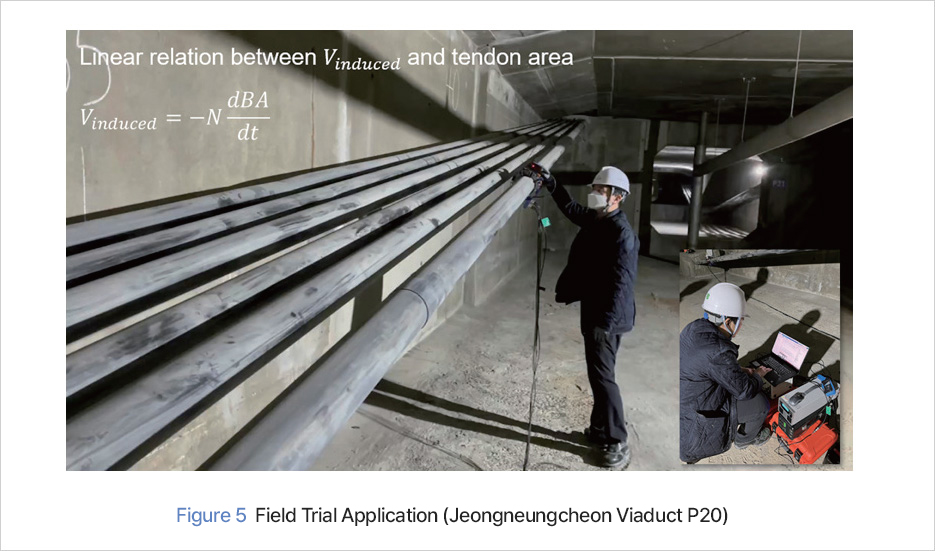
Decision-making Technology Using Signal Processing and Artificial Intelligence
Figure 6 shows the results applied to the specimens made to test the developed non-destructive equipment. The cross-sectional area simulating the damage as well as the damaged section are schematized at the top of the Figure. The result, measured by the same process as in Figure 5, is shown as the green line in Figure 6, but it is difficult to distinguish with the naked eyes because the amplitude change is insignificant. When the measured signal goes through several stages of signal processing, such as amplitude demodulation, to help assess the integrity of the external PS tendon using the measurements from the magnetic sensor, the result shown in the red line in Figure 6 can be obtained. In the red line, it can be seen that the change according to the damage to the PS tendon is clearly distinguished. However, a lot of experience is needed to distinguish whether these changes are caused by damage or noise. In addition, it is difficult to obtain information about the extent of the damage. To solve this problem, we developed an algorithm that uses a shallow FRP nerve sensor to specify the location of the damage, as shown in the blue dot in Figure 6, and predicts the ratio of the damage cross-section and even the length of the damage. Moreover, a number of specimens, as shown in Figure 7, were made and used to study artificial intelligence.
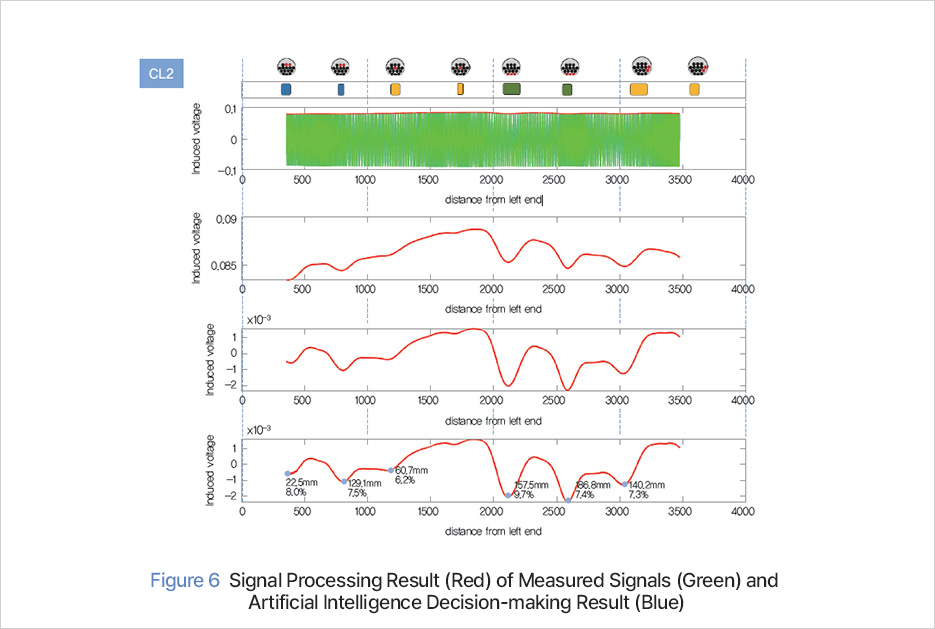
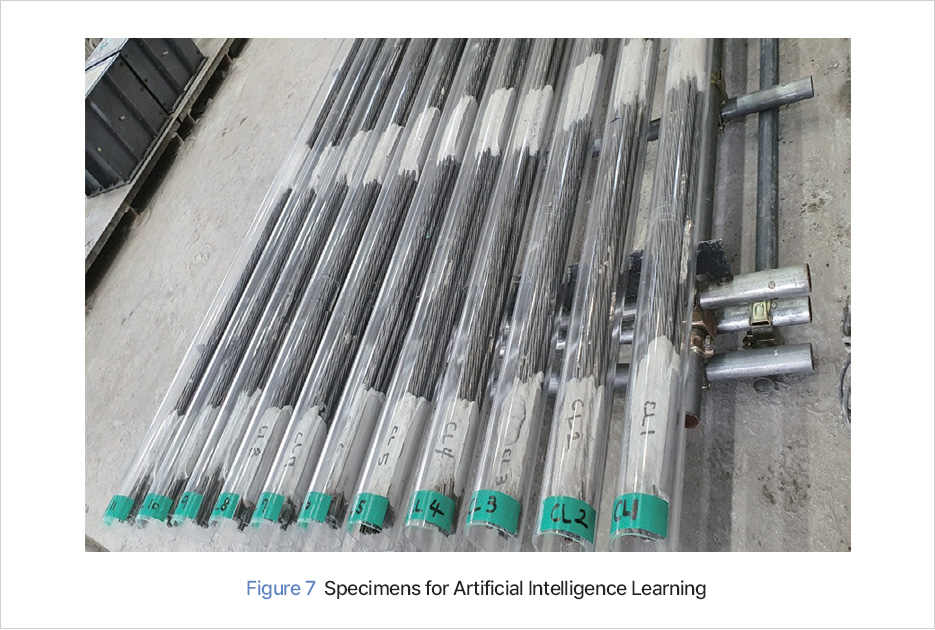
Epilogue
The KICT has developed a technology for nondestructive testing of the external PS tendon, a major element of the PSC structure, to prevent situations such as the Jeongneungcheon Viaduct that occurred in 2016 from being repeated. This technology uses the principle of nondestructive testing of the cross-sectional area made of metal with the application of electromagnetism and enables the repair and reinforcement of the PSC structure by detecting breaks and corrosion of the external PS tendon in advance. We not only developed sensors but also developed technology to help decision-making by improving the usability of sensors and applying signal processing and artificial intelligence to measured signals. The usability of the sensor is continuously improving through close communication with the companies currently in demand. Also, in the case of signal processing and artificial intelligence to help decision making, the algorithm is being enhanced and the accuracy is increased by adding learning data. We are also developing technology for the nondestructive testing of cables in cable bridges using the same principle. If the technology introduced here is completed and enters the bridge maintenance market, it will be possible to prevent huge economic losses through preemptive maintenance of bridges and to help avoid social losses caused by inconvenience to many people.