Development of Environmental Simulator and Advanced Construction Technologies Over TRL6 in Extreme Conditions
Development of Environmental Simulator and Advanced Construction Technologies Over TRL6 in Extreme Conditions
▲ Senior Research Fellow Shin Hyu-soung, KICT Department of Future & Smart Construction Research
Prologue
In May 2021, South Korea became the 10th participating country in the “Artemis Accords” project, an international piloted lunar exploration program led by NASA. As not only the United States but also Europe, China, Japan, and India have announced plans for lunar exploration, it feels as if the dream of space construction which had previously seemed far away has become more concrete. Furthermore, looking at Korea, which has not yet performed a concrete mission, it even makes one feel impatient to think that Korea may be falling behind again.
The recent discovery of large amounts of ice in the lunar poles has accelerated the competition for lunar exploration. This is because ice not only can provide fuel for rockets, but also water and oxygen, which are essential for sustaining the life of astronauts. The Moon's gravity is only one-sixth that of the Earth's, which makes it easier to get out of the gravisphere with relatively little fuel. Therefore, the usability of the Moon as a stopover is growing, because space missions can depart from the Earth, recharge their fuel on the Moon, and take off to deep space such as Mars. In addition, since the Moon is close to the Earth, it is a good place to prepare various technologies to be used in outer space and on other planets and to conduct various scientific studies, which further increases the value of the Moon. All of these are reasons why many countries around the world intend to build bases on the Moon and use them for the long-term residence of astronauts.
The Korea Institute of Civil Engineering and Building Technology (KICT) has been leading space construction research through the BIG Project since 2016. To strategically respond to the shifts in the space development paradigm caused by the efforts of nations around the globe, such as space base construction and resource development, this study aims to secure core construction technologies applicable in outer space, an ultra-extreme environment. Centering on the achievements of the 6th year (2021) of the study, this article aims to introduce the development status of the four core technologies in detail: Development of a full-scale chamber for realizing extraterrestrial planetary ground environment and verification technology; infrastructure construction technology using extraterrestrial planetary local materials; technology for the informatization of space for construction on the ground of planets; as well as the development of planetary ground investigation equipment and the planetary underground informatization technology.
Development of a Full-scale Chamber for Realizing Extraterrestrial Planetary Ground Environment and Verification Technology
The Full-Scale Dusty Thermal Vacuum Chamber (DTVC), which simulates the extreme lunar surface environment, is used to minimize the risk of failure in the real extraterrestrial space environment by verifying various technologies and equipment developed for lunar exploration. This DTVC was made in 2017 and installed in the Future Convergence Building, and was completed in 2019 after undergoing a stabilization test. The internal scale of DTVC is 50 m3, and it can simulate the temperature (from -190 ℃ to +150 ℃) and vacuum conditions (exclusive of ground: 10-6 mbar, Inclusive of ground: 10-4 mbar) of the lunar surface, and a large amount of lunar simulant is put inside the chamber to evaluate the impact of cosmic dust, etc. (Figure 1).
The Dirty Thermal Vacuum Chamber (DTVC)'s performance in creating vacuum and temperature environments has been secured through studies in Years 1 through 5. In 2021, studies were carried out for the simulation of ground temperature conditions according to the lunar night and day conditions; the measurement of the thermal conductivity of the ground according to the vacuum pressure for creating the ice ground; as well as the system for simulating electrostatic charging environments on the lunar surface and its measurement study.
As the lunar surface has no atmosphere, the temperature near the equator can rise to 120 °C during the day, and can drop to as low as -170 °C at night. However, since the thermal conductivity of lunar simulant is low in a vacuum environment, the temperature change of the soils below 10 cm depth is not large, and the low-temperature state is maintained. The soil temperature according to the depth in the low/high-temperature environment of the full-scale chamber constructed based on these data was measured (Figure 2), and further study will continue to improve the performance of simulating the temperature of the ground.
In addition to temperature and vacuum, the characteristic lunar surface environmental condition is electrical, which shows a positive potential of less than +20 V under the influence of sunlight during the day and a negative potential of hundreds to thousands of V at night under the influence of the Earth's plasma (Figure 3). This characteristic is considered a threat to the long-term residence of astronauts and equipment on the lunar surface, and it is necessary to understand and develop technologies to address it.
To simulate this electrical environment in the DTVC, an electrification environment simulation system using ultraviolet lamps and electron beams was built in a small vacuum chamber (Figure 4). Based on the electrical data on the lunar surface, a similar environmental simulation and a measurement method were devised.
In this year, the 7th year of the DTVC, a study on ground cooling in the chamber and measuring the potential of the ground charged with static electricity in an electrical electrification environment will be conducted. Through such research, it is planned to advance the environmental simulation performance of the DTVC and develop it into a more reliable construction technology verification facility in the lunar environment.
Infrastructure Construction Technology Using Local Materials of Extraterrestrial Planets
To build a lunar base, construction materials are needed. As the cost of transporting such materials from the Earth to the Moon would be astronomical, it is essential to develop a technology that makes it possible to produce construction materials using resources available on the Moon. To this end, a study is being conducted to solidify the “Lunar Simulant,” local resources available on the Moon, through a microwave-sintering technology in order to use it as a construction material.
Sintered pellets of lunar simulants are created when lunar simulants (KLS-1) are densified at a temperature of 1,080°C or higher through the microwave-sintering method, and the density and compressive strength of the sintered pellets are increased as the sintering temperature rises. The thermal expansion characteristics of all materials used in the construction of the lunar base are very important, as repeated contraction and expansion of construction materials with the extreme temperature change of the Moon can cause cracks in the structure. The thermal expansion coefficient of the sintered pellets of lunar simulants produced by the microwave sintering method is about 5 × 10-6 °C-1 within a range similar to the lunar surface temperature (from -100 to 200 ℃), which was confirmed as similar to the thermal expansion coefficient of actual lunar rock. In addition, the thermal expansion coefficient of the sintered pellets of the lunar simulants did not change significantly even after processes of heating-cooling-reheating, so it was confirmed that the microwave sintered lunar simulant had high thermal resistance even under the Moon’s extreme temperature changes.
To use the sintered pellets of the lunar simulant as a lunar base construction material, it is first necessary to review their homogeneity. In this study, the porosity was estimated through the Statistical Phase Fraction (SPF) method using X-ray CT images of the sintered pellets of lunar simulant to evaluate the homogeneity based on the porosity distribution of the material. It was confirmed that the total porosity of the sintered pellet of lunar simulants, estimated by the SPF method, was almost identical to the porosity calculated through the density analysis. Through estimating the local porosity of the local sintered pellets by dividing the CT image of the sintered pellet of lunar simulants into unit cells with a constant volume, it was confirmed that the mean porosity of 1,080 ℃ and 1,100 ℃ sintered pellets of lunar simulants were 30.4±2.1% and 27.1±2.9%, respectively, and distributed in the ranges of 26-40% and 20-36%. At the same height, the porosity decreases from the outside to the inside of the sintered pellet. This is due to the characteristics of microwave heating, which has a higher internal than external temperature, and it can be seen that a denser structure is formed in the center of the sample.
Currently, sintered block of lunar simulant is being manufactured to increase its utility as a construction material, and to apply microwave sintering technology to a real lunar high vacuum environment, microwave vacuum sintering equipment must be built and sintering experiments conducted.
Technology for Informatization of Space for Construction on Extraterrestrial Planetary Ground
To select the optimal site for the construction of a lunar base, a lunar topography survey is essential. However, Global Positioning System (GPS) is not available on the Moon, and the Moon's Permanently Shadowed Regions are low illuminance areas without sunlight. Therefore, this study aimed to develop a real-time 3D topographical information technology based on an unpiloted vehicle that can be used to construct the high-precision 3D topographic map required for design and construction on the lunar surface.
In this study, research was conducted to acquire real-time three-dimensional topographic information in low illuminance and GPU-shadowed environments by using a sensor combination of a stereo camera mounted on an unpiloted vehicle and an Inertial Measurement Unit (IMU). In particular, a self-supervised CNN-based image enhancement module was developed to maximize mapping performance in a low illuminance environment, and mapping performance with a mean error of less than 7 cm in a low illuminance environment was secured. In addition, simulated planetary topography consisting of craters, rocks, hills, soil, and gravel areas was built in the KICT's indoor simulated terrain laboratory and SOC Demonstration Research Center (Yeoncheon), and verification experiments for unpiloted topography informatization technology were conducted (Figure 7).
The research was conducted on object recognition in images of constructed simulated extraterrestrial planetary topography, region classification, and evaluation of the similarity of the same object in other images. To automatically classify objects and regions of interest in the targeted areas, a topography and terrain feature recognition and region classification technique using Mask R-CNN, an open source program for deep learning region recognition, was developed. We also developed a matching method for identical object and terrain features in multiple images using the Triplet network, and completed a major object matching system between aerial photos and unpiloted-vehicle topographic images (Figure 8). In the future, we plan to develop a GIS-based unpiloted topography informatization technology system by improving the accuracy of unpiloted topography informatization technology and artificial intelligence object matching technique and combining them.
Development of Extraterrestrial Planetary Ground Investigation Equipment and Extraterrestrial Planetary Underground Informatization Technology
Moon explorations, which had stalled for a while after humans first successfully landed on the Moon, began to become active again when the existence of ice at the lunar poles was confirmed. To analyze the ice and underground resources that exist at the poles of the Moon, drilling equipment must be mounted on the exploratory Lander or Rover. In order to transport and operate such equipment on the Moon, an extreme environment, requirements in terms of small size, light weight, low power, high efficiency, and high performance have to be met. In this study, a prototype of drilling equipment that can be operated in atmospheric pressure and low temperature environments was first developed. In addition, in consideration of transportation needs, miniaturization of 0.27 m3 grade, weight reduction of 18.5 kg grade, and low power consumption of 44.4 W grade were secured. Prototype drilling equipment was pre-verified using artificial ice in the freezing chamber, and a field study was conducted under low power, low reaction, and waterless conditions for sea ice and frozen soils around the Jang Bogo Research Station to evaluate the drilling performance and identify problems in drilling the sea ice frost heaving (Figure 9). By performing the drilling performance and reliability evaluation under various local conditions, it was confirmed that drilling failure due to slip of the bit-cutting area occurred when the vertical reaction was 25 N or less, and drilling failure due to jamming occurred when it was 125 N or more. In the range of vertical reaction of 50 to 100 N and rotation speed of 25 to 125 rpm, drilling reliability of at least 60% was secured.
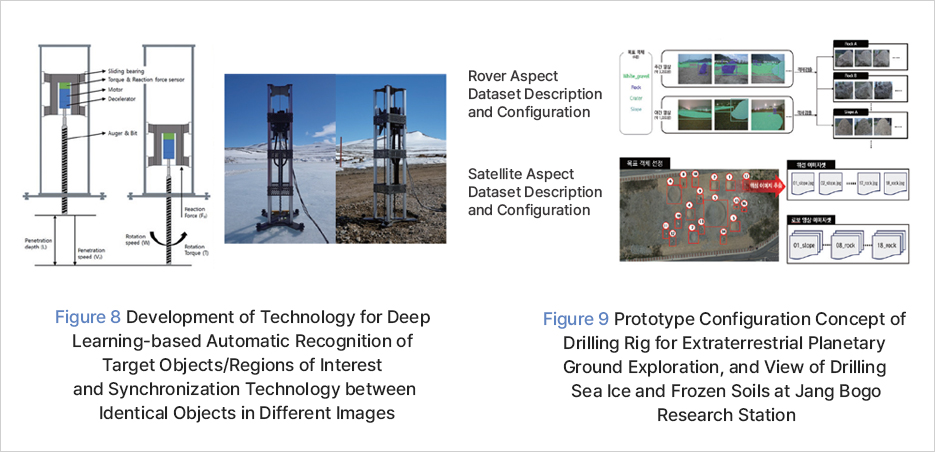
Epilogue
The construction of a space base, a dream of humankind for decades, is gradually becoming a reality. Space powers are competing with each other in terms of piloted lunar exploration and base construction plans to be the first to occupy the Moon. Relatively speaking, Korea's space development research lags far behind. However, the space construction field, which has just taken its first steps, has relatively low entry barriers compared to other space fields. As such, simply by securing the core technologies Korea can enter the ranks of advanced countries at the forefront of space exploration. It is hoped that the space construction technology developed by the KICT will be the first core technology to open the gates, and that it will leap forward as an institution leading the global space construction field in the future.